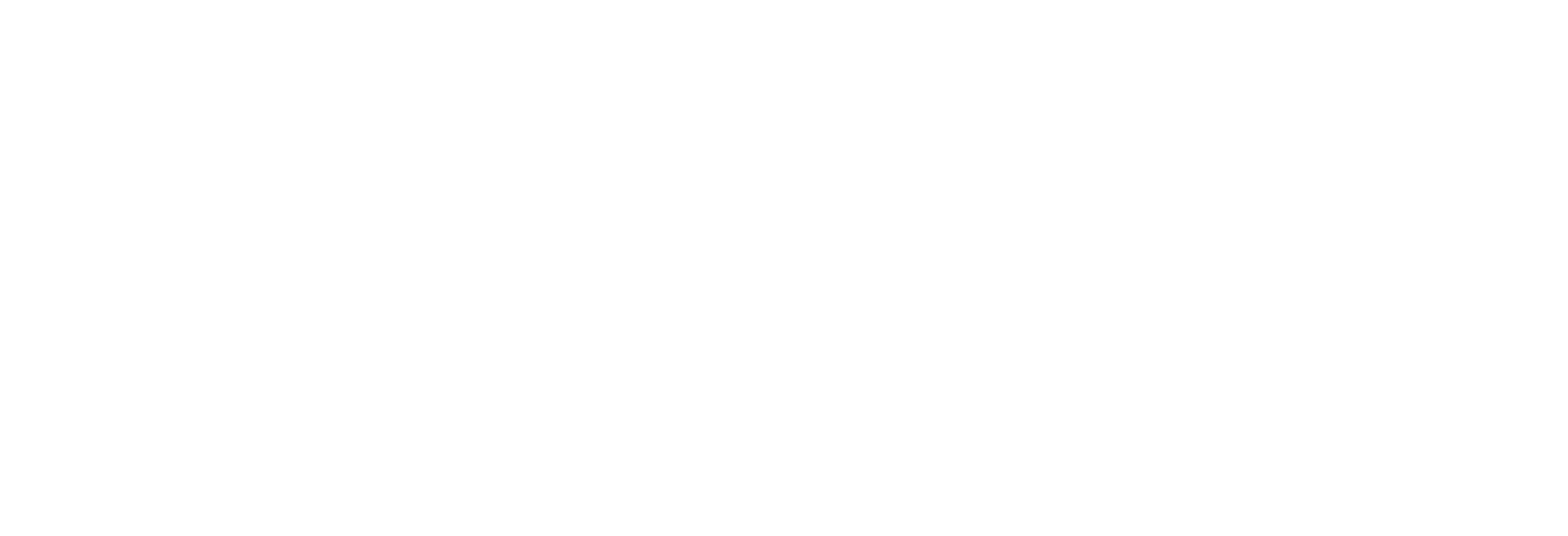
We offer quality construction services for custom home design to high-end home builders and general construction services in California.
In an era where the construction industry is constantly evolving and demanding greater efficiency, accelerated timelines, and heightened sustainability, prefabricated construction has emerged as a groundbreaking solution. Prefabrication, also known as modular or offsite construction, has revolutionized the way buildings are constructed by fabricating building components in a controlled factory environment before they are transported and assembled on-site. This innovative approach offers a plethora of benefits, including increased efficiency, improved quality, and significant cost savings. In this blog post, we will explore the remarkable rise of prefabricated construction and its profound impact on the modern building industry.
The construction sector has long grappled with challenges such as prolonged project timelines, unpredictable weather conditions, and wasteful practices. Prefabricated construction provides a dynamic and efficient alternative that addresses these challenges head-on. By shifting the construction process from traditional on-site methodologies to a controlled factory environment, prefabrication unlocks unparalleled advantages that resonate with the industry's evolving needs.
Prefabricated construction is a catalyst for transforming the construction process, leading to enhanced efficiency and accelerated project timelines. This approach allows for the simultaneous fabrication of building components alongside site preparation, saving invaluable time and compressing project schedules. The controlled factory environment ensures optimal conditions for manufacturing, maximizing productivity and minimizing waste. Unlike conventional construction, prefabrication diminishes weather-related delays as on-site assembly can progress unhindered by external conditions. This streamlined efficiency not only expedites project completion but also boosts overall productivity, enabling occupants to access finished structures in a fraction of the time.
Prefabricated construction places an unwavering focus on precision engineering and stringent quality control, resulting in exceptional building quality. Advanced technologies such as computer-aided design (CAD) and computer numerical control (CNC) machinery ensure precise measurements and accurate assembly of building components. The controlled factory environment enables rigorous inspections and thorough testing, guaranteeing consistent and superior quality throughout the manufacturing process. As a result, prefabricated buildings often exhibit unparalleled craftsmanship, fewer defects, and enhanced structural integrity compared to traditional construction methods. The marriage of technology and quality control ensures that prefabricated construction meets and exceeds the highest industry standards.
Prefabricated construction presents compelling cost savings throughout the project lifecycle. By streamlining the manufacturing process, labor requirements and associated costs are significantly reduced, delivering enhanced cost predictability for project stakeholders. The accelerated project completion timeline also translates into reduced financing costs. Additionally, the controlled factory environment fosters efficient material utilization, minimizing waste and lowering material costs. Furthermore, prefabricated construction leverages economies of scale in the production of standardized building components, further contributing to cost savings. These cost advantages position prefabricated construction as a highly economical alternative to traditional construction methods, appealing to developers and project owners seeking optimized financial outcomes.
Prefabricated construction aligns seamlessly with sustainability goals by actively reducing waste generation and promoting energy efficiency. The precise manufacturing process minimizes material waste by employing accurate measurements and optimized material usage. Waste materials can be responsibly recycled or disposed of within the controlled factory environment, ensuring sustainable waste management practices. Furthermore, energy-efficient approaches can be seamlessly integrated into the manufacturing process, employing energy-efficient machinery and sustainable building materials. By prioritizing waste reduction and energy efficiency, prefabricated construction contributes to the creation of a greener, more sustainable built environment.
Contrary to prevailing misconceptions, prefabricated construction offers a wealth of design flexibility and adaptability. Modern prefabrication techniques empower architects and designers to realize customized designs and modular configurations that meet diverse architectural requirements. Advanced technologies, such as Building Information Modeling (BIM), enable accurate visualization and customization during the design phase. Furthermore, prefabricated components can be easily modified, relocated, or expanded, ensuring future adaptability and scalability. This inherent flexibility ensures that prefabricated buildings can effortlessly accommodate evolving needs and changes throughout their lifespan.
The rapid rise of prefabricated construction marks a transformative wave sweeping through the building industry. With its enhanced efficiency, improved quality, and substantial cost savings, prefabrication has become a viable and attractive alternative to traditional construction methods. By embracing prefabricated construction, the industry can overcome long-standing challenges and embrace a future where construction projects are delivered with unmatched efficiency, exceptional quality, and remarkable sustainability. As the demand for faster, smarter, and greener construction practices intensifies, prefabricated construction stands at the forefront of innovation, poised to reshape the way we build and pave the way for a more prosperous and sustainable future.